博客分享|影响叶轮机加工时长的设计因素
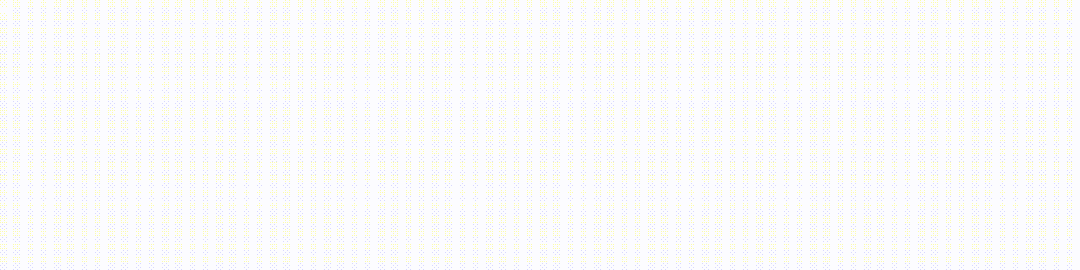
叶轮的形式(如侧刃铣叶轮还是点铣叶轮;半开式叶轮还是闭式叶轮;整体铣式叶轮还是焊接式叶轮)决定了它的基本制造工艺。但除了这些基本形式外,还有一些设计特征会显著影响其制造工艺和加工时长。这些设计特征包括:
通常叶轮通道最窄的点在轮毂部位,这需要细长的铣削刀具,而细长的铣削刀具加工速度慢。因此,最小通道宽度会影响铣削速度。最小通道宽度由叶片数及轮毂处的最小半径决定。另外,虽然最小宽度是一个很好的判别指标;但我们建议最好进行全面的三维检查,以确保加工刀具可以通过整个流道(该检查过程可以由我司MAX-PAC模块完成)。
高的叶片需要更长的加工刀具,而长的加工刀具加工速度较慢(因为长的加工刀具在加工过程中更容易受力偏离)。叶片高度越高,切削面积越大,需要去除的材料体积也越大。叶片厚度与高度的比值也是一个重要因素。高而薄的叶片在加工时容易产生偏移形变,在侧刃铣的情况下这种现象更明显。这种情况下,如果不能采用一些补偿措施(如额外的半精加工或形变补偿),那么就会造成最终加工成品误差增加。震颤导致的加工面质量低也可能是由薄叶片引起的。
较小的圆角半径通常有利于叶轮的气动性能,但并不利于结构和加工。更小的圆角需要更小的加工刀具(必须使用半径不大于最小圆角的球头刀),因此也需要更多的铣削时间。可变的圆角可在局部调整叶根半径,但需要较小的加工刀具和更多刀路,因此会增加加工时间。
钝边的尾缘最容易加工,因为它无需铣削。圆形的尾缘可以是简单形式定义的,也可以定义为椭圆和沿叶高变化半径、椭圆度等更复杂的形状。对于这种非钝边的尾缘若要求侧刃铣,最好能保证其与叶片压力面、吸力面之间过渡光顺、连续。这样可以保证在侧刃铣时,其叶身和尾缘可以用一个连续的刀路完成。
当一个直纹面的叶片拥有一个圆形进出口边缘,且该边缘与叶片侧边的直线元相交,那么所得的边缘则是非直纹面。这个非直纹面的边缘需要点铣(如下左侧图所示)。如果该边弯曲的不明显,那么可以用很小的偏差将其重构为一个直纹面(如下右侧图所示)。需要注意的是,在重构时不能强行让叶片吸力面、压力面与前缘相交处的直线元突然变为与前缘的直线元方向一致。因为这可能影响加工时的机械稳定性并使得侧刃铣质量降低。对于这种情况,正确的处理方式是对前缘的切割、生成应独立进行,以形成更光顺分布的直线元。设计时微调前缘椭圆的椭圆度也是改善这一情况的有效手段。
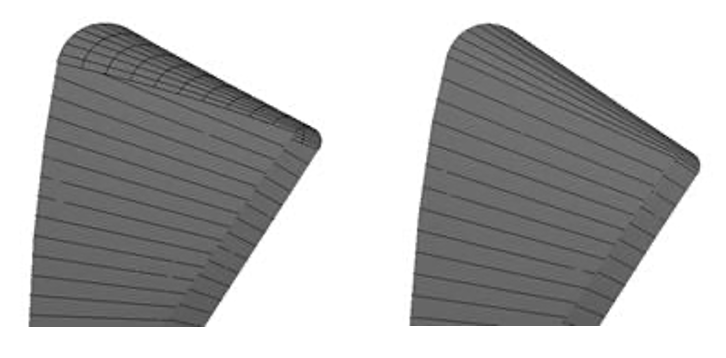
前缘与叶片直线元匹配不佳(左图)
前缘与叶片直线元匹配良好(右图)
分流叶片的前缘通常为后掠的结构。这样做的好处是避免分流叶片前缘叶尖部太薄且有利于产生更光顺的刀路。总体而言,若进出口叶片角不变,那么设计点气动性能也不会发生明显改变。然而需要注意的是,直线元分布变化会影响通道面积等三维几何特征,从而导致阻塞裕度及振动频率发生变化。

直线元与分流叶片前缘对齐的例子(左图)
后掠的分流叶片前缘及其对应的刀具运动方向(右图)
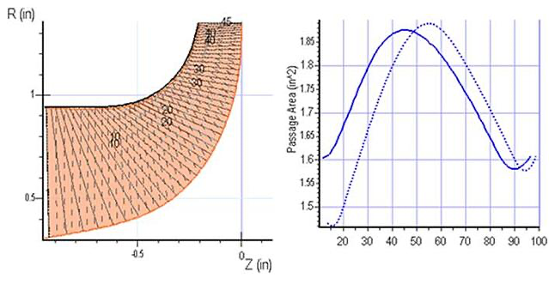
直线元分布对于压缩机通流面积的影响

直线元匹配对于压缩机振动频率的影响
球头铣刀对叶轮加工后,会在叶片表面留下刀痕。残留高度的尺寸由刀具的尺寸和刀路数决定。这些残留对机组性能的影响一直是很多会议和论文讨论的主题。一个研究的重要结论是:在很多情况下,合适的残留可以提高叶轮的效率。在设计点附近尤其如此(因为设计点时,气流往往与残留刀痕方向一致)。但在非设计点时,刀痕的影响尚不明确(可以确定的是非设计点时,刀痕的尖端对跨越主流方向的二次流会产生影响)。目前在机匣处理中已有类似的结构来控制失速。
确定最佳刀痕残留高度的关键因素是附面层的相对厚度。可以根据附面层粘性子层的厚度来确定大致最佳刀痕残留高度。可以用CFD来量化预测边界层厚度,以此来确定最佳刀痕残留高度。在最终采用这种措施时应该谨慎,因为刀纹带来的性能提升往往是有限的,而不合适的刀痕(如选择的刀痕残留高度过大)产生的负面影响却很大。
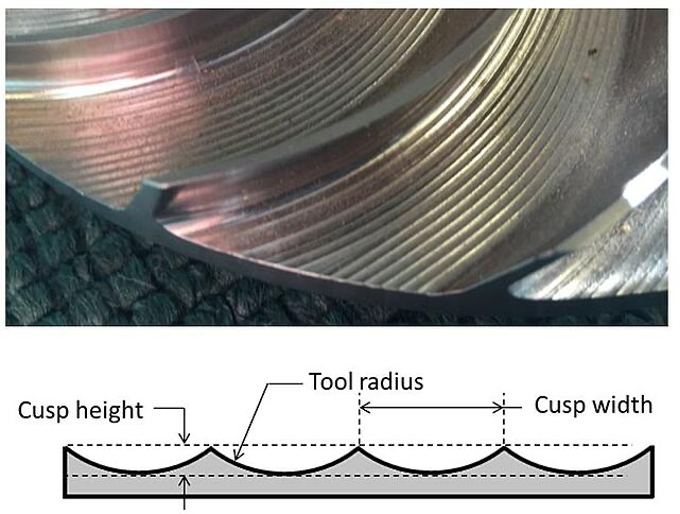
由球头铣刀产生的轮毂面刀痕
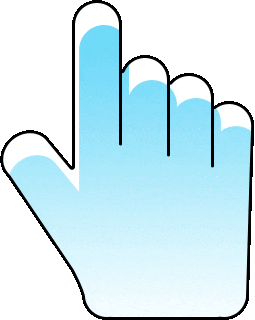
可以用需要加工叶轮的关键几何参数来估算加工时间。估算结果需要根据实际车间加工的信息不断修正,不同的车间估算的结果可能不同。这些估算的公式往往比较简洁,但其背后需要大量部件的切削时长的数据库支撑。显然,切削时间也与生产资料及加工人员的经验水平有关。基于以上原因,这些加工时间的估算方法基本是定制化的,是专用的。下图是一个实际的加工时间估算程序实例。

估算五轴加工切削时间的程序示例

尽管增材制造饱受关注,但在其被广泛应用于许多涡轮机械应用之前,仍有大量实际问题需要解决。这些问题包括:残余应力水平,尺寸精度,以及产生的材料性能。最终产品的整体公差和质量也是一个问题,因为增材制造得到的叶轮机械的主流道区域往往不够光顺。为了解决这个问题,通常需要额外的常规制造工艺(与增材制造做加法不同,传统制造工艺是做减法)来达到足够的表面光洁度。简而言之,增材制造虽然很有前途,但短期内不会取代传统方法。传统的制造方法有很多优势,至少对于传统的零件来说是这样。
增材制造的真正优势在于它能够生产传统方法无法制造的部件。增材制造还需要新的软件、新的分析方法、新的设计范例来释放其潜力。Concepts NREC正在为几个客户进行增材制造,并将所获得的知识整合到我们的产品和服务中。
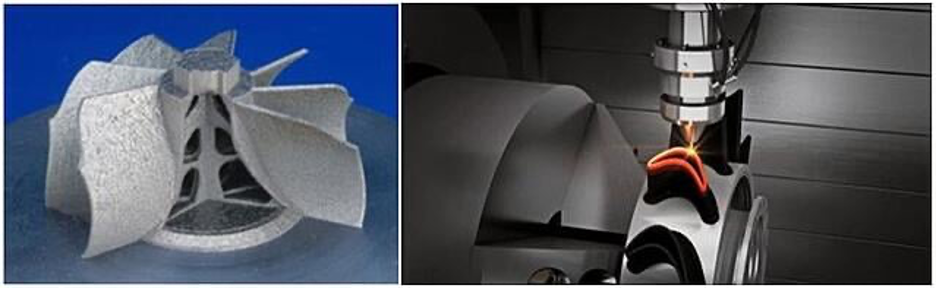
增材制造的向心涡轮(左)和轴流涡轮叶片(右)由德国亚琛弗劳恩霍夫工业研究所和德马吉森精机有限公司提供。
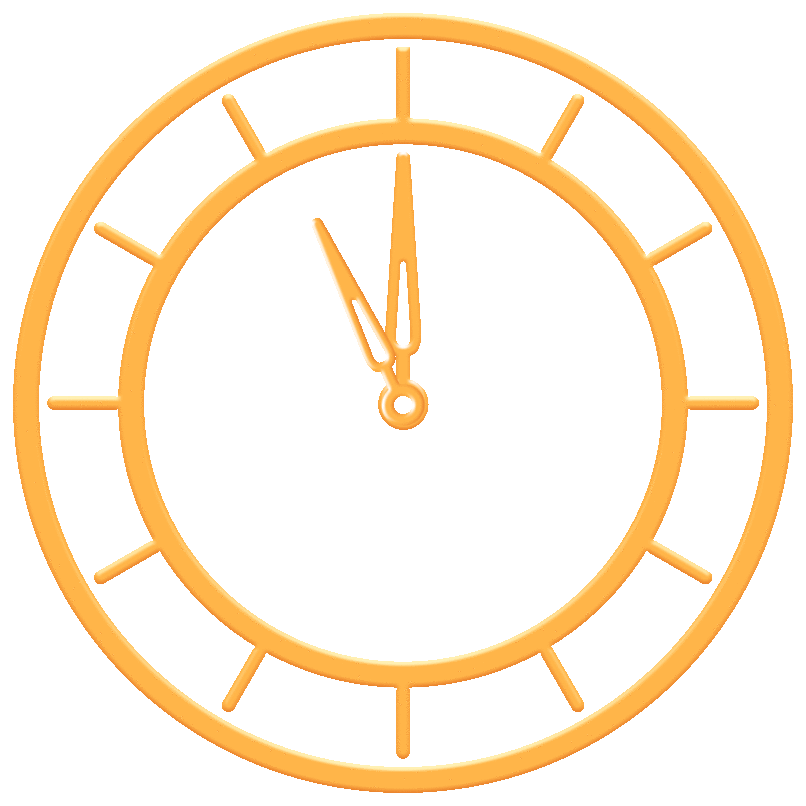
CONCEPTS NREC BLOG

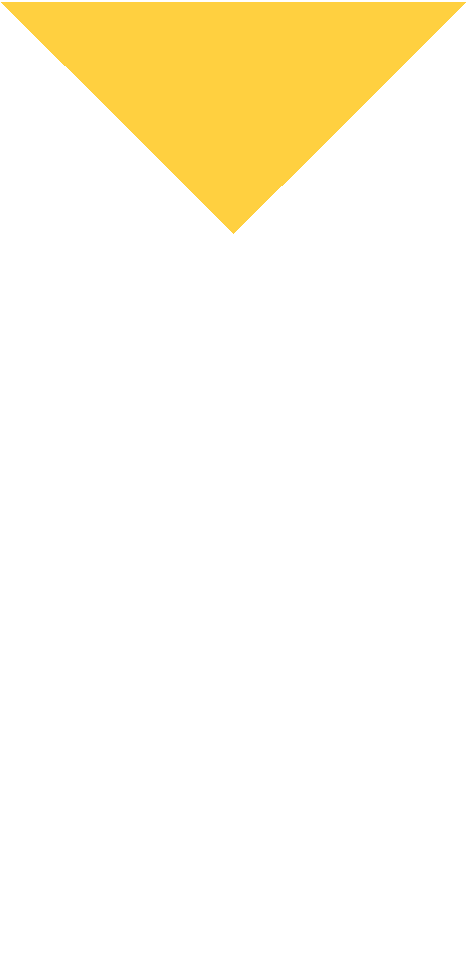
Mark R. Anderson|供稿
Mark R. Anderson,Concepts NREC首席技术官
宋威|译
何道贵|校
王娜欣|编辑
自1956年诞生以来,Concepts NREC就立足于叶轮机械设计领域,以其深厚的技术底蕴与不断创新的精神,推出了一系列集创新、品质和性能于一体的解决方案。正是这样的坚守和专注,为我们打造了无数改变世界的杰出产品与理念。无论是为清洁高效的再生能源和发电技术提供支持,还是助力航空航天事业迈向更高峰,我们始终走在时代的前沿,引领可持续发展。进一步了解Concepts NREC的精彩世界,敬请访问www.conceptsnrec.com。
软件 / 工程 / 硬件 / 培训
博客分享|探索高效低汽蚀泵诱导轮的优化之道
博客分享|基先进的真实气体模型
版权所有 © 概创机械设计(上海)有限公司
沪ICP备19046901号
联系我们
快速进入
友情链接